Canadian architecture and multi-disciplinary practice Dialog has designed a hybrid mass timber tower prototype that promises to revolutionise tall buildings as we know them. The patent-pending design that can be used to produce hybrid timber towers of up to 105 storeys will also be zero-carbon, addressing one of the world’s most pressing issues: climate change.
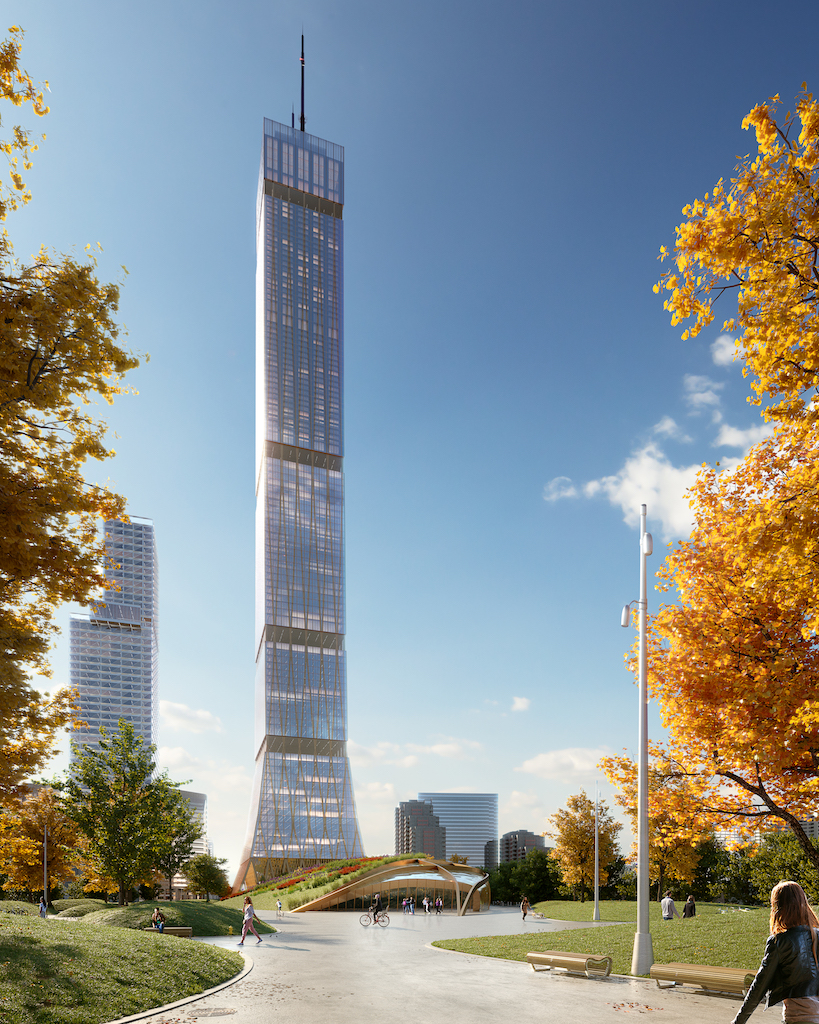
Dialog’s prototype Hybrid Timber Floor System (HTFS) would use a unique combination of sustainably-harvested timber, steel, and concrete. The system will allow for hybrid wood buildings around the world with fewer support columns and beams, resulting in more spacious floorplates, which can be built to much greater heights. The result will be cleaner, visually-striking towers that will fight pollution rather than cause it. DE51GN speaks to Dialog’s Craig Applegath, principal, architecture and Thomas Wu, principal, structural engineering, to shed light on the groundbreaking technology behind the idea.
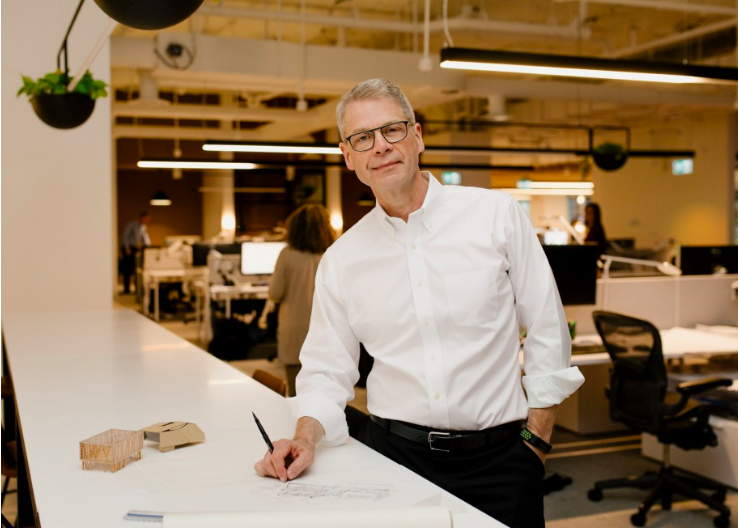
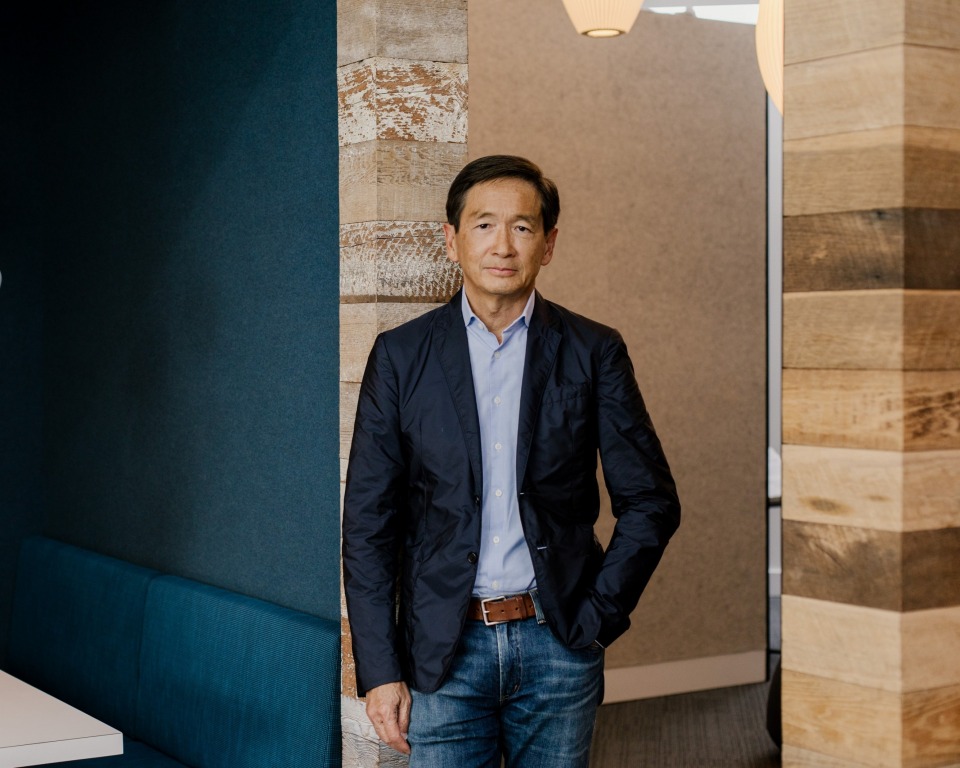
How did the HTFS concept come about?
Craig Applegath (CA): At Dialog, our expertise spans engineering, structural and mechanical engineering, architecture, and planning and there were two things that were compelling us to think. One of them was the impact of carbon emission on climate change. Construction, operation and manufacturing are responsible for 39% of the carbon production in a building.
We have a lot of responsibility as designers. So we thought what can we do to contribute to this challenge in a positive way. In the last few years, around the world, especially in North America and Europe, mass timber has been emerging as an opportunity for building in a way that locks up carbon. It also creates beautiful buildings.
But there are big challenges with wood which are the inherent nature of its structural properties. Thomas (Wu) is a structural engineer who has worked on many of our big buildings in the US and Canada. His expertise is in tall buildings. Then we have another principal of structural engineering, Daria Khachi, whose expertise lies in wood. We got together and thought about how to build a very tall building with wood but one that is commercially viable. Most medium-scale or even a supertall timber building is possible to build structurally but it might not be commercially viable on a per sq ft cost basis. It’s one and a half or two times as expensive because you have to use so much wood to support the wood above it. We started to explore these problems to come up with a strategy to design tall buildings with mass timber but at the same time recognising the realities of its structural intricacies.
The other big challenge that had us thinking was how do we make this a zero-carbon tower. It was not something that was being done already. Over a period of two years, we developed a number of strategies and put them into this prototype tower, and it’s what you see now.
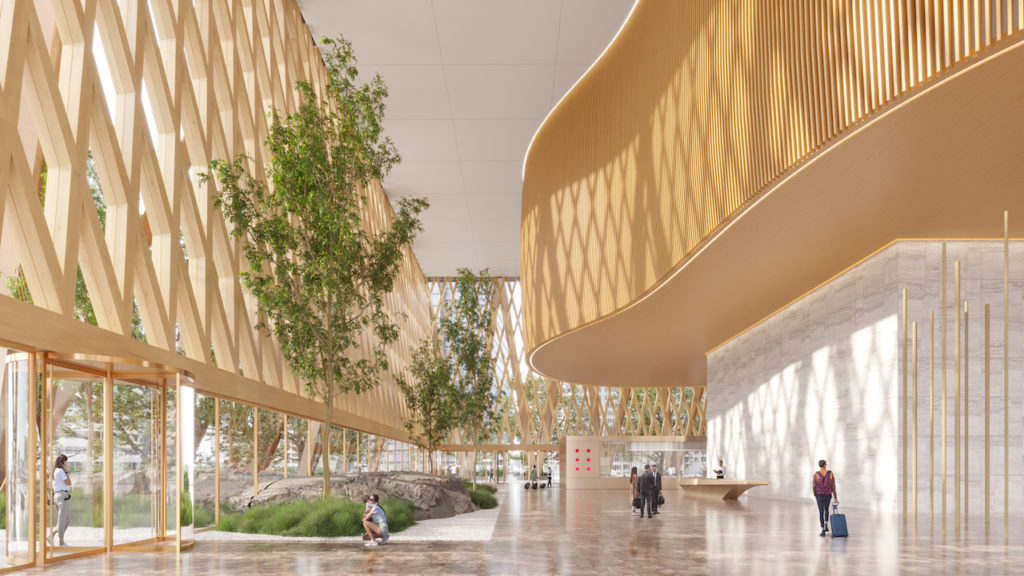
What structural challenges did you encounter while designing this hybrid prototype?
Thomas Wu (TW): One of the challenges on this building was achieving the span. People prefer the open span. They don’t like to enter buildings and see columns in the middle of the space. It’s not good either for circulation, partition, and for dividing the space. The building owners always prefer to have a clear expanse so they can customise it to their requirements.
Clearly, any wooden beam or drop beam support can only have a span of 30ft maximum. What we’re working with is mass wood called CLT – cross-laminated wood. It’s made out of sawn timber that is stacked up in formations of 2×6 or 2×4 to create a long span. That’s what is available in North America for mass timber construction.
But it has limitations and the maximum mass span is 20ft, otherwise the wood will be inefficient. In our workshop, we are constantly trying to push boundaries. With my expertise in concrete and steel, I said why don’t we put the two together. Combine high-strength steel embedded into concrete encasing that goes in the underbelly of the wood.
We, then, ran innumerable manual calculations until my hands were tired, before switching over to a spreadsheet. Then I passed the idea over to other studios for them to peer review my calculations. It seemed to work and suddenly the possibilities began to look real and fascinating. CLT is largely sawn timber that has been cured and dried but it’s never 100% dry. It retains at least 20% or more moisture in the wood.
During the cycle of the building, CLT itself will get internal cracks. So we wanted to use recycled wood to proof the building.
CA: Another thing we did at the workshop was to team up with a construction firm Ellis Don. What they brought to the table was how we could manufacture the wooden panels offsite and bring them to the site on trucks and then swing them up on cranes. That helped us to define the panelling strategy that was 12ft wide 40ft long which is the maximum you can bring on a truck. That became the panel structure that Thomas and Daria worked on and embedded it with those post-tension steel tendons to provide it with the strength it needs to span that distance.
TW: It’s prefabbed and trucked to the site. The speed of construction is critical in supertall buildings.
CA: The idea was that this material is going to be very good for the spanning in the floor material but in a tall building, you need the concrete core, and the steel diagrid frame on the outside to get the height you need. But 70% of the materials used in the building are used in the floor system, so we could use 70% wood in the building plus the tendons in the floor system that allowed us to use the maximum amount of wood in a building. Ellis Don demonstrated that it would cost no more than doing a combination of steel and concrete. All of a sudden, we came to the conclusion that wood is no longer something that is not economically viable. This was one of the most important challenges in using wood – having a developer confident enough in its economic viability to take it on.
It’s an extremely elegant strategy and apparently, no one has done this before. No one has created a panel that can span 40ft – typically CLT spans only 30ft.
TW: There was another hurdle that we had to overcome for any supertall building – fire. It is a big issue. If you put a lot of wood in a building, people often question whether it can withstand forces such as a fire. Keep in mind, we have a concrete encasement in the underbelly of the wood panel. The wood itself is 12 inches thick and the concrete band is non-combustible. It is designed in accordance with the fire rating guidelines. The wood panel has been researched and it has been through the burn test. Once you burn or put the wood under two-hour fire test, the charred layer is 3 inches thick at the most. The charred layer then acts as the protective layer and protects the rest of the wood. It is self-extinguishing because there is no oxygen that can penetrate into the charred layer. We’re still undergoing more fire testing as well as structural testing.
“We ran innumerable manual calculations [to test the strength of the wood] until my hands were tired, before switching over to a spreadsheet. Then I passed the idea over to other studios for them to peer review my calculations. It seemed to work and suddenly the possibilities began to look real and fascinating.”
Thomas Wu, principal, structural engineering, Dialog
What other findings did you come across while working on this prototype?
CA: The developer we are collaborating with shared that one of the value propositions of CLT is that potential leasers figured that tenants desire wood. So not only does it solve the carbon problem but it actually improves the rental potential of the property. They were, in fact, impressed that they could have wood and it wouldn’t be more expensive.
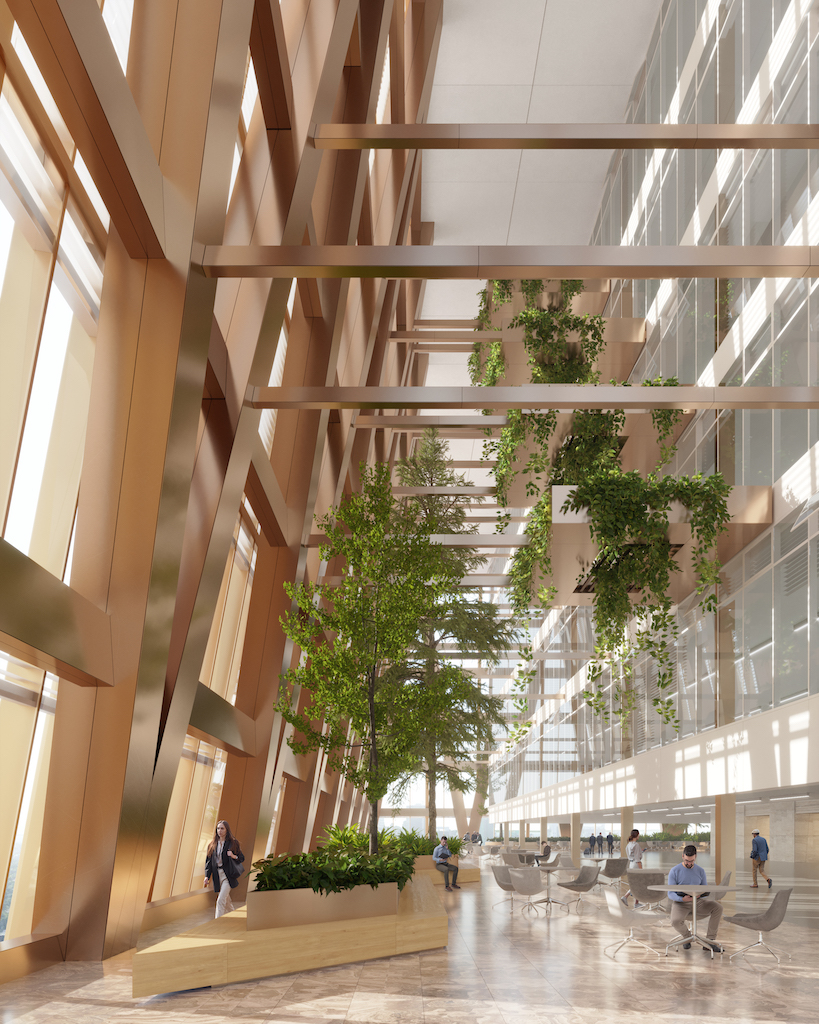
What are some of the building maintenance rigours required of wood?
TW: We don’t expect maintenance to be an issue. The HTFS would have a concrete topping, which is a very important layer of the structure. It bonds mechanically with the CLT, so what you’re walking on is actually a concrete surface and you’re exposing the belly of the wood that is the ceiling. In most office buildings, you have raised floor, so very low maintenance is required. And the only time you will need access to the ceiling is if you’re doing any maintenance work on the electrical and plumbing systems. Also, around the perimeter of the building is structural steel which protects the entire building.
How about its durability in hot and humid and harsh arid environments?
TW: For example, Malaysia and Indonesia are also timber-producing countries. They produce hardwood and they also produce other types of timber for construction. In any type of office setting, you will be in a controlled environment, which is similar to any building in, say, North America. In any tall to supertall building, you have redundancy of mechanical system.
CA: The humidity in such controlled environments in office buildings is always around 25 to 30 per cent. In fact, Thomas and Daria have been exploring the possibility of using hardwood, the kind available in Asia, which is even better. So there is an opportunity to use different types of wood with the same strategy.
TW: In fact, we have been thinking about LVL, laminated veneer lumber or cross-laminated mass plywood. In Oregon, there is a factory, that produces such a type of wood as building construction material. Mass plywood is a more stable type of wood.
CA: And the best part about this laminated wood is that you can use any type of wood to make it.
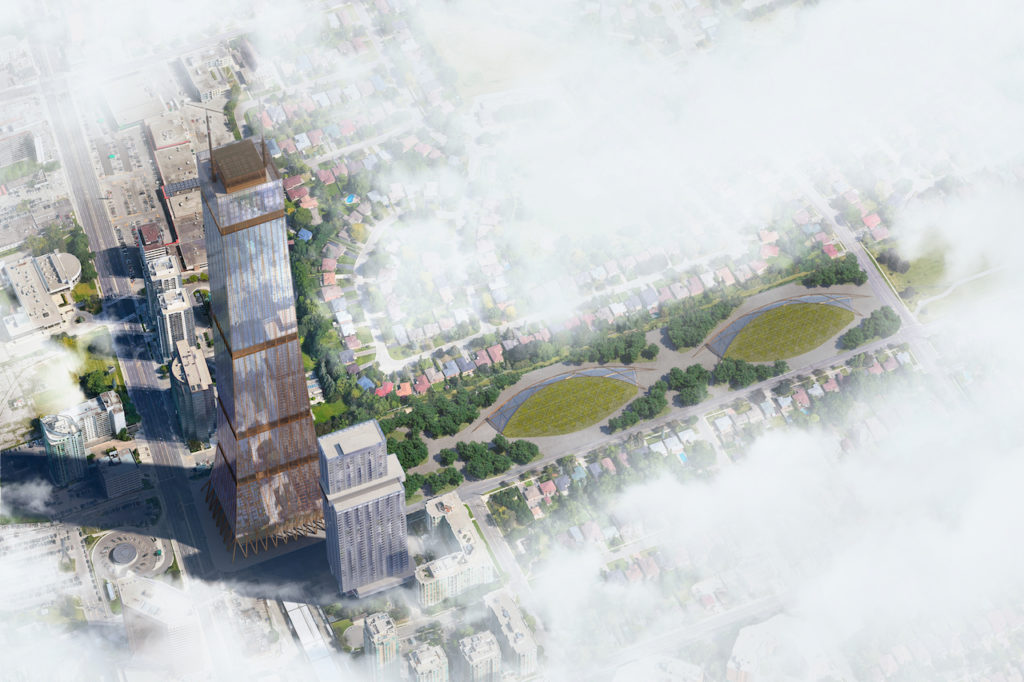
If there is so much innovation in the field of wood as a building material, why aren’t more developers and stakeholders embracing it since there are so many cost benefits as well? Why are they still skeptical?
TW: Because at the moment, we are testing uncharted waters and what we are proposing is still expensive. It’s a new system and most builders aren’t concerned about the environment but the bottom line. But the climate change crisis has intensified to an extent that we see an opportunity to effect a real change through responsible design strategies. Until someone takes a stand and says that we have a solution and let’s collectively think about the results, no one is going to move ahead. So here we are, sticking our necks out.
CA: The other really cool thing about it is that it’s zero-carbon and this is a very innovative technology that integrates photovoltaics into the building facade. So on the east and west sides of the building, there is photovoltaics in the facade that generate 20 to 25% of the power required by the building. Then we have a co-generation plan below the main level which produces heat – we’re in the northern hemisphere so heat is essential – and electricity from natural gas. But natural gas, upon burning, produces carbon dioxide. So what we have is a liquified gas (LG) bioreactor, where blue gas goes into a water tank with LG and very intense light, and the LG eats up the carbon dioxide and turns into more LG and that can be filtered and sold for a profit. You take a pollutant and turn it into something that is a valuable product. The building becomes zero-carbon, plus produces a valuable product, and it’s made from wood. It’s quite an amazing combination of technologies altogether.
“We are testing uncharted waters and what we are proposing is still expensive, until it’s embraced on a mass scale. It’s a new system and most builders aren’t concerned about the environment, but the bottom line. But the climate change crisis has intensified to an extent that we see an opportunity to effect a real change through responsible design strategies. Until someone takes a stand and says that we have a solution and let’s collectively think about the results, no one is going to move ahead. So here we are, sticking our necks out.”
Thomas Wu, principal, structural engineering, Dialog
Can adaptive reuse buildings adopt this set of technologies in the process of restoration or extension?
CA: There are two approaches to that question. The first is you could use the technology that Thomas and Daria have developed to add floors or extensions. It doesn’t necessarily have to be for tall buildings only. The reason we did it for the tall building is that it enhances the value proposition. We wouldn’t be having this discussion if we were implementing this technology in a four-storey building. We have named it Beacon of Hope, as it’s aimed at the future, and its height reflects that it’s the building of the future.
While you could use the HTFS, you could also use the generation system. In Asia especially, there’s limited space to build. So while existing buildings can be updated, there’s also a need to build new buildings. If you’re going to build tall, the question then arises about how to do it in a responsible way. Building tall makes sense in dense cities.
You could use the [HTFS] technology to add floors or extensions. It doesn’t necessarily have to be for tall buildings only. The reason we did it with a tall building is because it enhances the value proposition. We wouldn’t be having this discussion if we were implementing this technology in a four-storey building. We have named it Beacon of Hope, as it’s aimed at the future, and its height reflects that it’s the building of the future.
Craig Applegath, principal, architecture, Dialog
What are some of the parameters to gauge the performance of the building over a course of time?
CA: You calculate the amount of energy required to heat and power up the building which will produce a specific amount of carbon and take that carbon and feed it to the bioreactors to take the carbon out. It’s a rather simple formula.
Does it require any special type of site studies?
CA: One of the opportunities, if you put a building like this on a site, is that you could become the hub to power the neighbourhood or plug it into a smart grid. Because such buildings can be designed to produce additional power if required.
TW: It doesn’t really matter where you put our floor system. The tower will be designed to suit a specific geographic area. So for example, in Singapore, factors to take into consideration would be high-wind and earthquake, in Hong Kong, it’ll be typhoons. The study is not about how tall we can go but it’s a demonstration in a tall building environment to make a provocative statement.
CA: During the discussion process with Thomas, we did surmise that this design could be used in different situations by changing the various parts of the diagrid and the truss structures that tied it to the core.
TW: Same principles apply to any tall building around the world. Every geographic area will have different diametric requirements. The system itself remains unchanged unless you change the floor load requirements.
Where and when do you anticipate this kind of building to be constructed first?
We’re already talking to a developer in Toronto to use a similar technology but for a smaller building. It’s a 40-storey building that can’t go any higher because of the zoning issues. But they really liked the structural strategy to get the aforementioned long span and the zero-carbon approach. I reckon Asia is looking at taller buildings with a greater interest than North America. The only cities in North America where it might make sense to go high are Toronto and New York City.
In Singapore, the height limit is about 280m. I think Singapore will be a great city because most of your buildings are so green already. We’re hoping that the first building will be in Singapore.
TW: The system could be manufactured/prefabbed anywhere in the world. You don’t have to ship the panels. You could have a warehouse and you can manufacture it there itself.
Do the prefab panels require special equipment?
TW: Eventually, it will. We’re currently in the prototype stage, we haven’t yet started mass quantity production. The question is how fast can we get the wood to the factory. For example, if you’re talking about Dubai, we will need to consider where is the closest source of wood which could be Europe; what kind of wood, whether it’s wood chips or sawn lumber. All that has to be factored in before we can design in mass quantity. Eventually, the process is repetitive and the taller or bigger the building, the more panels you’d require for mass production. Only robotic equipment could manufacture them at a fast pace, else it’ll get too labour intensive.
You might also like:
Vincent Callebaut unveils design for modular timber tower in Cebu City